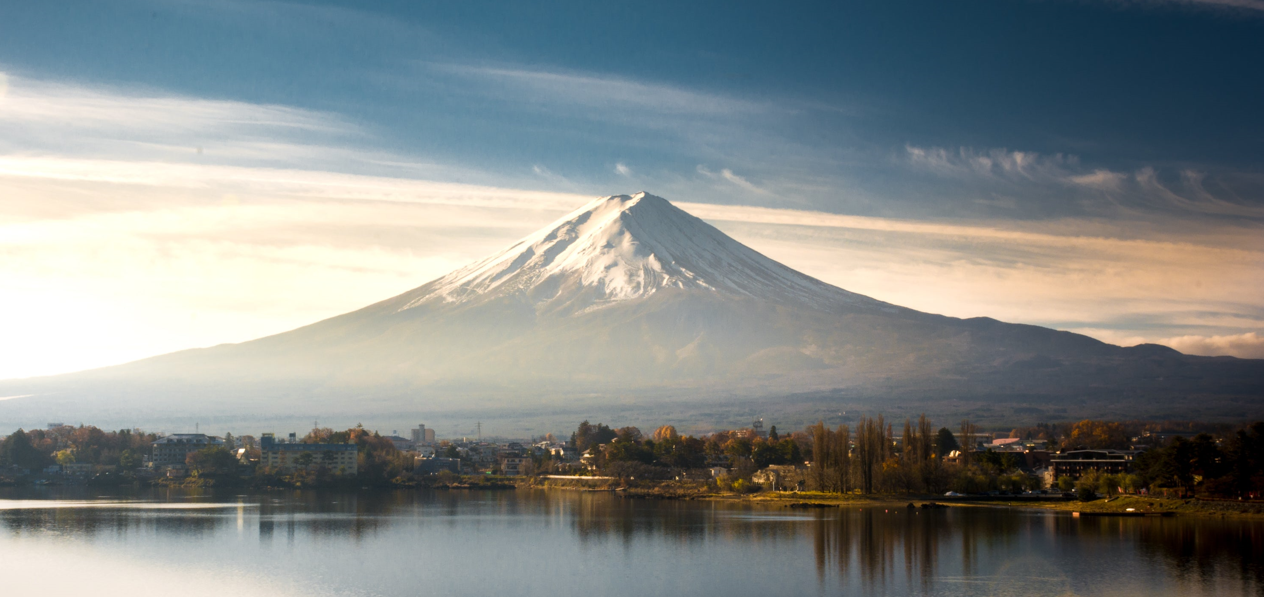
-
Sakai Traditional Craftsmen Collection
-
The Japanese knives crafted by the artisans of Sakai City boast over 600 years of history and tradition. We promise to deliver this exceptional quality to our customers.
-
Traditional Craftsperson Qualifications and Requirements
-
In Sakai City, only 28 traditional craftsmen carry the responsibility of preserving Japan's proud heritage of craftsmanship. These artisans earn the prestigious title of traditional craftsman after more than 12 years of hands-on experience and passing stringent examinations. The knives they create represent centuries of skill and tradition. Compared to mass-produced alternatives, knives forged by KIREAJI’s traditional craftsmen offer superior quality and practicality, and the title of traditional craftsman has become a symbol of trust for those seeking true craftsmanship.
-
Traditional industries are founded on the accumulation of skills, passed down through generations and learned through dedicated practice with both hands and body. These techniques cannot be conveyed through words alone; they are refined over time, through years of experience and intuition. Today, more than ever, we recognize the immense challenges of preserving these traditions.

Forging
For the sake of sharpness, we discern even the slightest variations in color.
The Art of the Blacksmith
-
A blacksmith is more than just a metalworker — they are an artisan who transforms raw steel into high-performance tools through tradition, skill, and precision. It takes years of dedicated training to master this craft.
-
In Sakai City, Japan, blacksmiths heat steel to approximately 1,100°C and carefully hammer it to shape, refine, and strengthen the blade. This demanding process requires not only physical strength but also technical expertise and focus.
-
Each knife is forged by hand with careful attention to detail — from shaping the steel to applying the correct heat treatment. These techniques, refined over generations, ensure exceptional sharpness, durability, and balance.
-
While machines can mass-produce blades, only human hands can produce knives with true character and soul. Every strike of the hammer, every adjustment to the blade, reflects the experience and pride of the blacksmith.
Our mission is to carry this tradition forward — creating knives that not only perform exceptionally, but that chefs around the world can rely on for years to come.
In the end, it's not just a tool — it's a handcrafted work of precision, designed to elevate your cooking.
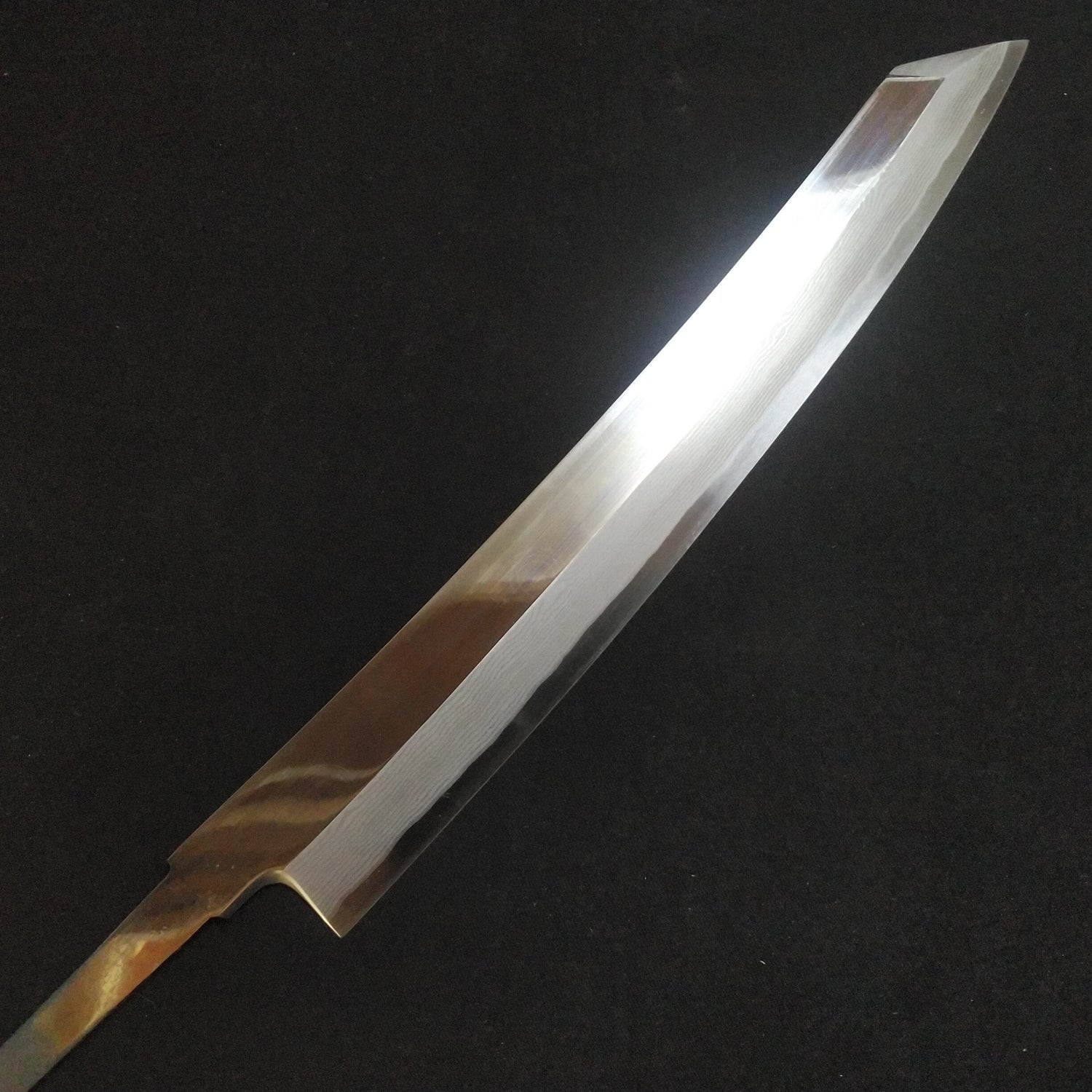
Shogo Yamatsuka
Japanese Knife Ginsan Craftsmanship
A master blacksmith renowned for his exceptional skill in forging Ginsan steel—a rarity in Sakai. Certified as a Traditional Craftsman in 2012, he is trusted by professional chefs for overseeing every step of knife-making, including final sharpening, with unwavering precision.
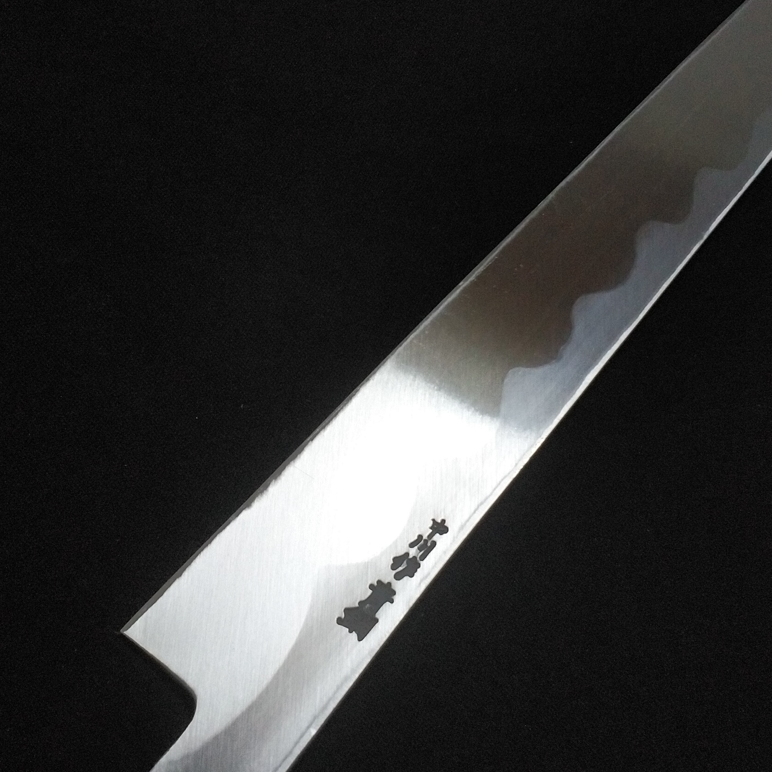
Satoshi Nakagawa
Japanese Knives by the Youngest Traditional Craftsman in History
The youngest Traditional Craftsman ever certified in Sakai. Recognized at age 30 for his outstanding forging skills, Nakagawa is a favorite among top Japanese and Western chefs. He is seen as a key figure leading the next generation of Sakai craftsmanship.

Keijiro Doi
A Master's Legacy
A legendary blacksmith from the esteemed Doi lineage in Sakai. He began his career at 19 and worked for decades before retiring in 2012 and passing away in 2017. His knives are no longer in production and are now highly prized collector’s items.
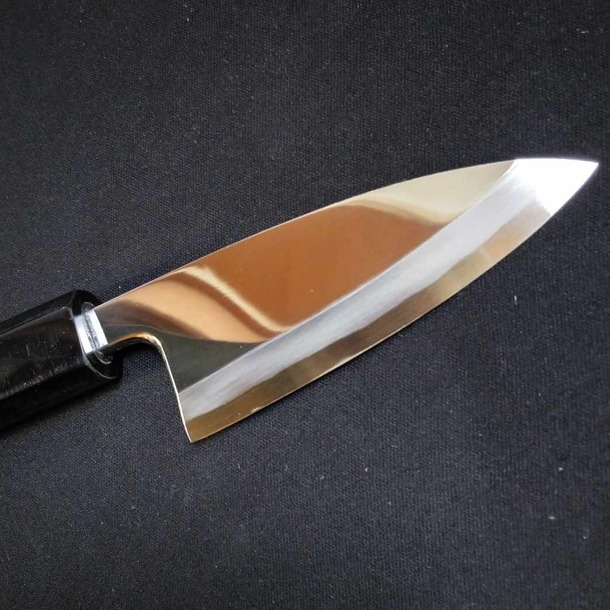
Tadashi Enami
Tradition Meets Innovation in Japanese Knives
The fifth-generation blacksmith of a workshop with over 600 years of tradition. Certified in 2003 as a Traditional Craftsman, Enami combines classic techniques with innovation to meet the evolving needs of today’s chefs.
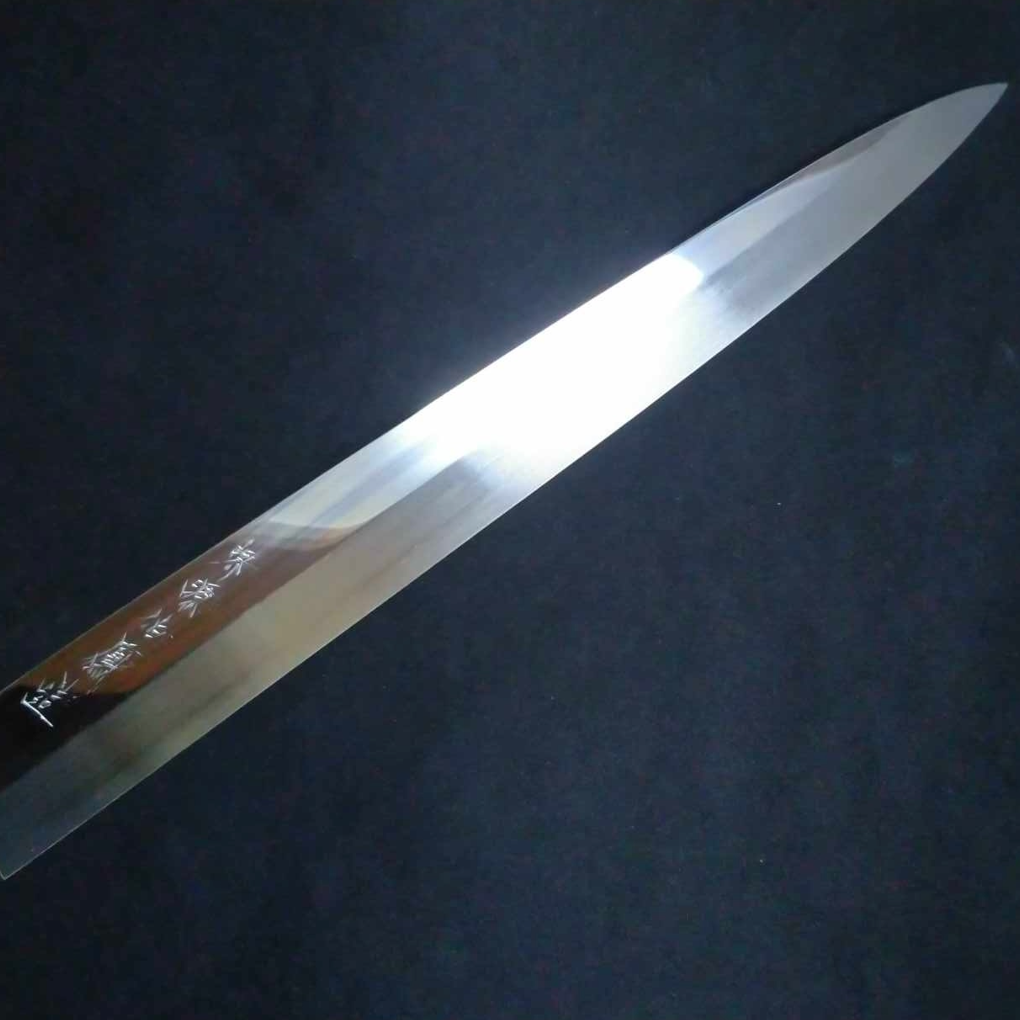
Yuzan
Legendary Traditional Craftsman of Japanese Knife: The Father of Traditional Craftsman Shogo Yamastuka
A legendary craftsman known for mastering Mizuyaki among Honyaki knives, considered one of the most difficult forging techniques. His rare, museum-worthy knives are no longer made. He passed on his skills to his son, Shogo Yamatsuka.

Kenichi Shiraki
Master of Sakai Forged Knives
A highly respected Traditional Craftsman known for his mastery of Sakai’s forging tradition. Having retired, his knives have become rare treasures. His sole apprentice, Satoshi Nakagawa, continues his legacy through Nakagawa Cutlery.
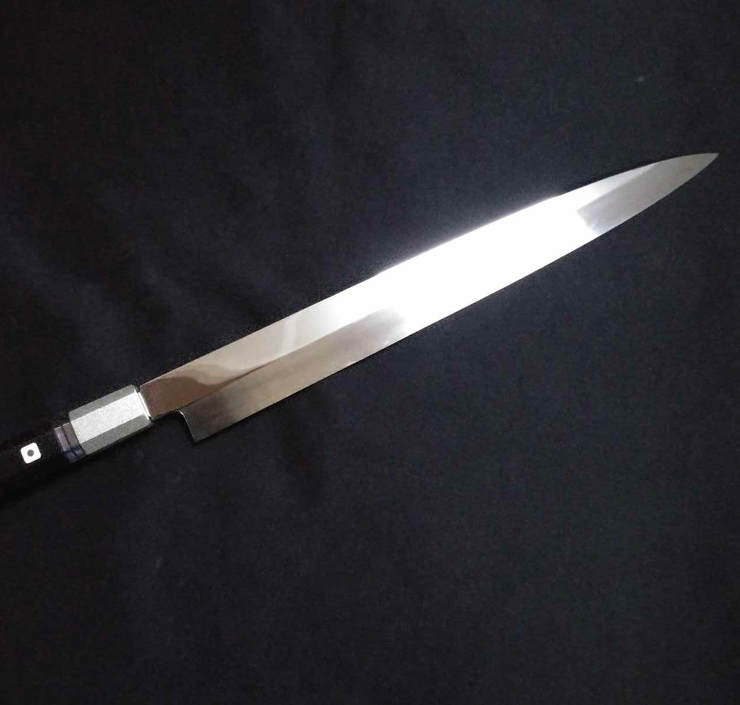
Tatsuo Ikeda
Master Craftsman Whose Knives Embody Skill and Passion
A pioneer in Japanese knife innovation. Certified in 1985 as a Traditional Craftsman, he developed the "Mon-Tanren" forging method and received the Order of the Sacred Treasure, Silver Rays, from the Emperor of Japan in 2009 for his lifetime achievements.

Yoshikazu Ikeda
A Master Preserving Tradition and Shaping the Future
Began forging in 1967 under his father and co-founded Ikeda Tanrensho in 1983. Certified as a Traditional Craftsman in 1988, he was honored with Osaka’s Outstanding Artisan Award in 2014. He remains committed to preserving and passing on Sakai’s heritage.

Sharpening
For the sake of sharpness, we hone down to microns.
The Craft of a Blade Sharpener
-
A blade sharpener is not just a technician, but a craftsman. Their skill is the result of years of dedicated training and hands-on experience. True mastery cannot be gained overnight—it takes patience, failure, and relentless practice.
Many sharpeners begin their journey as young apprentices, observing seasoned masters and learning through repetition. Over time, they develop their own unique style and technique.
-
Sharpening is more than a technical process—it’s a daily challenge that demands focus and sensitivity. Each knife has its own character. To bring out its full potential, the sharpener must read the blade, respect its individuality, and apply the perfect edge.
This craft thrives not only on individual skill but on the shared pride and healthy competition among artisans. By constantly refining their techniques, they create blades that meet the high expectations of chefs worldwide.
-
For a sharpener, the ultimate goal is simple: to deliver knives with the finest cutting performance. In every blade, they pour tradition, technique, and passion—supporting Japanese knife culture with their hands and heart.
The sharpeners of Sakai City, with over 600 years of history behind them, are recognized globally for their craftsmanship. Every knife they produce embodies meticulous skill and quiet pride—a true companion for those who love to cook.
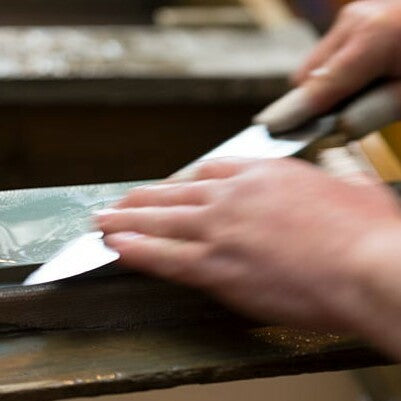
Tadayoshi Yamatsuka
Master of Japanese Knife Mirror Polishing
Certified as a Traditional Craftsman in 2022, Mr. Yamatsuka is highly regarded in Sakai for his exceptional mirror-polishing skills. His beautifully finished blades continue to captivate chefs both in Japan and around the world.
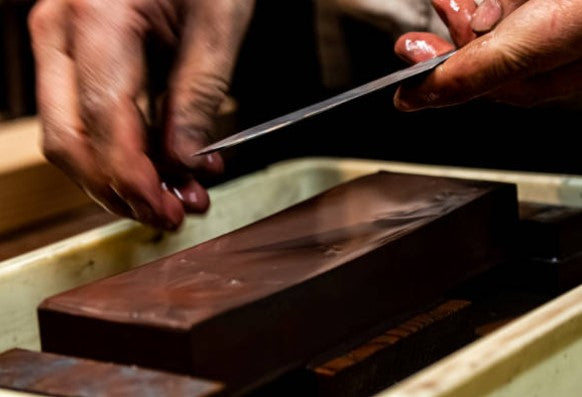
Shotaro Nomura
The Craftsmanship and Beauty of Sakai Knives
Mr. Nomura began his career in 1962 and was certified as a Traditional Craftsman in 1988. He honed his sharpening skills at the renowned Ino Hamono in Sakai and has since become a dedicated guardian of the city's time-honored knife-making traditions.

A knife is a lifelong investment — a reflection of the artisan’s daily dedication and craftsmanship.
Japanese knives are more than tools — they’re handcrafted works of art that connect you to the chef’s craft. With every use, you sharpen your skills and uncover the true flavor of each ingredient.
How Traditional Japanese Knife-Making Skills Are Passed Down
-
A Legacy Built Through Apprenticeship and Dedication
In the city of Sakai, the tradition of Japanese knife-making has been preserved and refined for centuries. This legacy is not sustained by manuals or textbooks, but through hands-on training, observation, and mentorship. The foundation of skill transmission lies in a time-honored apprenticeship system, where young craftsmen learn directly under experienced masters through years of disciplined practice.
-
Historically, the city and local knife associations established formal training centers for aspiring artisans to learn the basics. Even today, skills are passed down through these long-term apprenticeships, where daily repetition, attention to detail, and the spirit of craftsmanship are nurtured.
-
Learning by Watching: The Power of Observation and Oral Tradition
In traditional Japanese craftsmanship, skills are often transmitted through kuden (oral instruction) and mite nusu me—a phrase that literally means “steal by watching.” This method emphasizes observing the master’s techniques and intuitively grasping the delicate hand movements, rhythm, and sensitivity that define true craftsmanship.
-
Since many of the processes are still performed manually, mastering the subtle physical nuances—such as pressure, angle, and timing—is crucial. These are things that cannot be fully captured in writing or diagrams, making direct, in-person learning essential.
-
Support from the Community: Nurturing the Next Generation
The survival of this craft isn't left to tradition alone. The city of Sakai and industry organizations actively support skill transmission through subsidies, training programs, and certification systems such as the Dento Kogeishi (Traditional Craftsman) designation. This not only helps young artisans set clear goals but also enhances the social recognition of their work.
-
Thanks to these systems, the transition from novice to skilled craftsman is guided and supported, ensuring the continuation of high standards within the knife-making industry.
-
Education Through Experience, Not Classrooms
While systematic education through vocational schools is limited, real-world training under a master remains the primary route to becoming a craftsman. However, community outreach programs—including public workshops and factory tours—have helped spread awareness of the craft’s value among younger generations and the general public.
-
Preserving Unchanging Techniques in a Changing World
The techniques used in making Sakai knives have remained largely unchanged. Traditional hand-forging methods, natural whetstone sharpening, and careful handle fitting are still practiced today. Craftsmen continue to use traditional materials, such as straw for annealing and pine charcoal for water quenching, to maintain the integrity of the process.
-
These time-honored techniques, passed down through generations, are not preserved for nostalgia—they are preserved because they consistently produce knives of unparalleled quality. The pride that craftsmen take in their work forms the backbone of Sakai’s global reputation.
-
Conclusion — A Tradition Sustained by People and Community
The traditional craftsmanship of Sakai’s Japanese knives is sustained through a unique blend of long-term apprenticeship and the oral and observational techniques that have been passed down for generations. This is more than just skill transfer—it is a human connection built on trust, patience, and mutual respect.
-
At the same time, support from the local community and government organizations plays a vital role in keeping this heritage alive. With financial aid, training opportunities, and recognition programs, young artisans are given the tools and motivation to carry the torch forward.
-
Most importantly, the unchanging commitment to handcraftsmanship continues to define every knife made in Sakai. In a rapidly changing world, this dedication to tradition ensures that these knives retain their authenticity, quality, and cultural value. Backed by skill, pride, and the support of an entire community, the legacy of Sakai’s knife-making will continue to thrive for generations to come.

Why Do Professionals Choose Sakai Knives?
The secret is in theirunmatched sharpness, crafted fromcenturies-old techniquesblended withmodern innovation. The moment you hold one, your culinary passioncomes alive.

Sakai Uchihamono: The Ultimate Sharpness and Craftsmanship Forged by 600 Years of History
Sakai Uchihamono reflects a legacy of exquisite craftsmanship, embodying the art and tradition of blade-making in Sakai City through meticulous forging, sharpening, and handle attachment processes.

Sakai's Declining Japanese Knife Craftsmen
Sakai's esteemed cutlery tradition, renowned for its sharpness and craftsmanship, is at risk with only a dozen blacksmiths remaining. Facing competition and declining interest, strategies such as exploring new markets and fostering youth interest are vital for survival. This situation underscores a broader challenge in cultural preservation. Supporting Sakai’s craftsmen is crucial to maintaining this legacy.
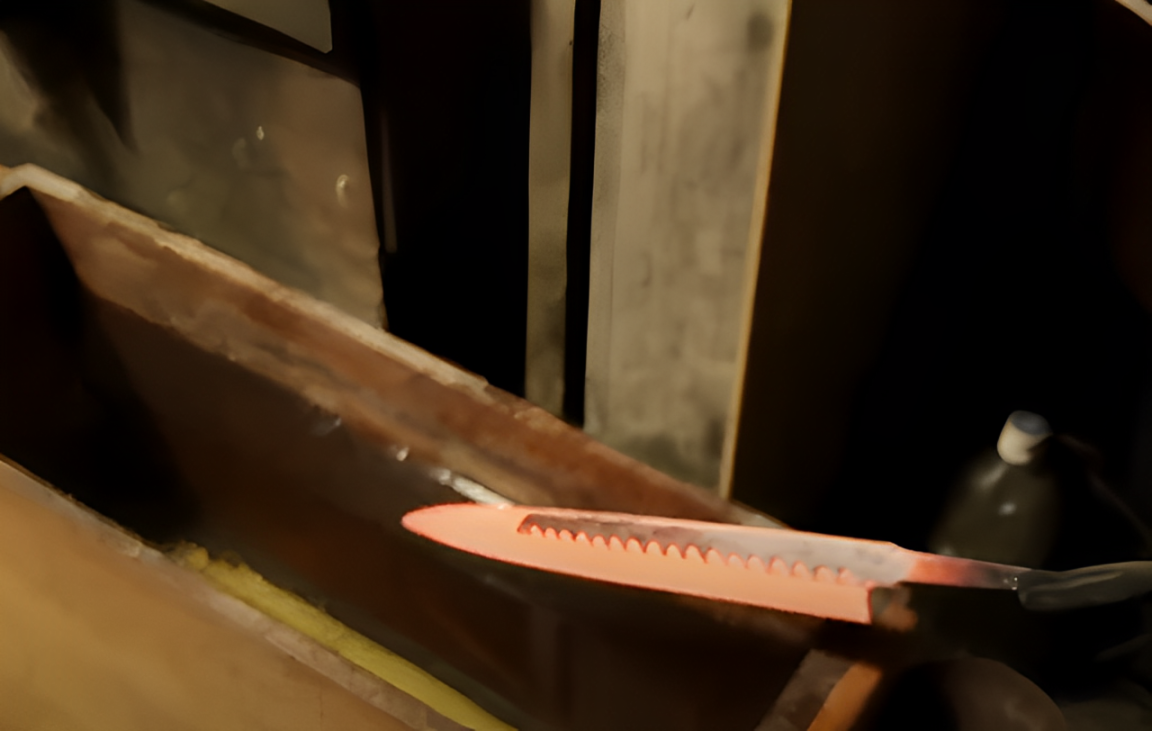
The Origin of Craftsmanship
-
The Artisan's Creed: Surpassing the Master
-
In the world of traditional craftsmanship, it is not enough to simply refine one's skills. The ultimate goal is to surpass the master. This is not just about achieving technical superiority; it is about creating new value that transcends the techniques and spirit instilled by the master.
-
When I began my journey, I could only follow in my master's footsteps. However, as I delved deeper into the art, I realized that merely imitating was insufficient. To "surpass" is to embody respect and gratitude for the master while pushing one's own abilities to their limits. It also carries the responsibility of inspiring the next generation with greater possibilities.
-
As a craftsman, I approach every knife I forge not as a mere tool, but as a crystallization of tradition and dedication. With this in mind, I return to the forge each day, ready to push boundaries further.
-
To those reading this, I want to share that every handcrafted piece bears the mark of such challenges and passion. Understanding this background can deepen your appreciation for the tools you hold in your hands.
-
Beware of Inexpensive Knives
Inexpensive knives are often made with cost-cutting measures during production. Specifically, important elements such as sharpness, balance, and maintainability—key factors that directly affect quality—are not given sufficient investment. These aspects are often difficult to notice at first glance, but they can significantly impact the performance of the knife.
-
At KIREAJI, we offer authentic Japanese knives crafted by trusted artisans from Sakai City. Every knife is carefully handcrafted with a focus on sharpness, balance, and maintainability, ensuring you receive a high-quality product that provides long-lasting reliability and peace of mind.